Innovation for Sustainability: Pioneering Low-carbon Manufacturing With Continuous Flow Chemistry Technology
This blog post was written by PharmaBlock, a leading provider of innovative chemistry products and services throughout the pharmaceutical R&D process and commercial manufacturing. Their services are available on the Scientist.com marketplace.
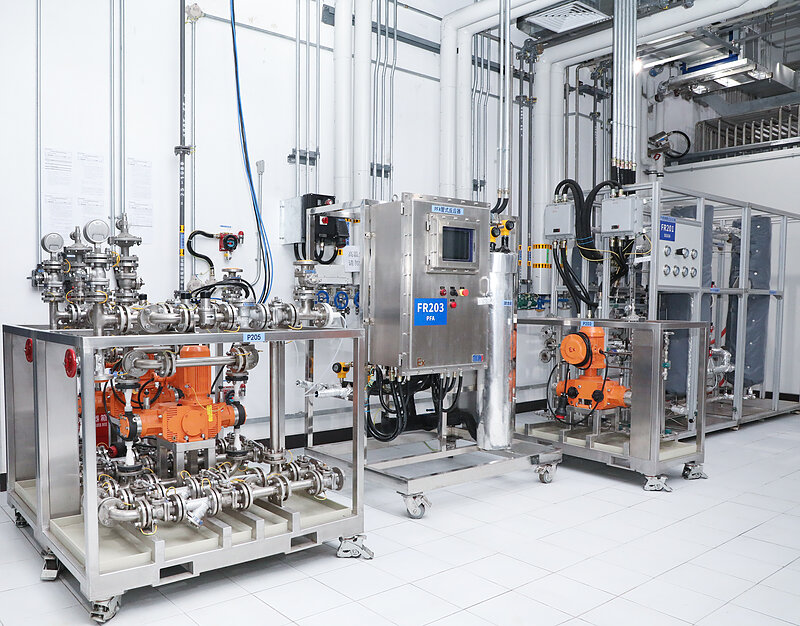
PharmaBlock is at the forefront of fostering sustainability in pharmaceutical development and manufacturing, with technology innovation serving as its core strategy. Continuous flow chemistry (CFC), one of the widely recognized green technologies, is celebrated for its ability to prevent waste generation, enhance energy efficiency and minimize the reliance on hazardous solvents, etc. However, the adoption of CFC has been hindered due to concerns over flexibility. PharmaBlock has successfully navigated these challenges through equipment innovations and an exceptional fusion of chemistry and engineering expertise.
PharmaBlock has applied CFC technology in more than 1800 development and commercial projects, including dozens of RSM in launched drug substances. It proudly stands as the exclusive CDMO recipient of the esteemed ACS Green Chemistry Award for two consecutive years, in both 2023 and 2024. The award-winning projects utilized the CFC processes to produce the key intermediates in multiple marketed drugs at MT scale, achieving significant improvements in energy efficiency, workspace utilization, safety and environmental sustainability with solid results. These cases exemplify PharmaBlock’s successful application of CFC technology and further demonstrate the value of CFC technology in enhancing sustainability in pharmaceutical production.
Innovation for Sustainability
Doing the Right Thing from the Beginning: The Core of Sustainability
PharmaBlock’s “Innovation for Sustainability” is a strategic response to the urgent market need for sustainable pharmaceutical practices that go beyond mere compliance with EHS regulations. Our core purpose is to embed environmental protection deeply into every aspect of pharmaceutical manufacturing through source design, utilizing cutting-edge technologies like CFC, ensuring that we are “Doing the Right Thing from the Beginning.”
The Leap from Lab to Manufacturing for Practical Sustainability
While CFC technology is gaining momentum, the core challenge resides in effectively implementing and scaling its application across the industry. PharmaBlock has taken the lead by not only widely adopting these technologies but also by innovatively designing versatile and robust equipment from research lab to commercial manufacture scale to meet pharmaceutical industrial needs.
Turning the Spotlight on Early Intermediates: Amplifying the Impact of Sustainability
Continuous flow manufacturing has found its footing in drug product and API production among major pharmaceutical companies. However, improving the environmental performance of raw materials and RSMs should not be overlooked as it offers the greatest sustainability return. These early intermediates often carry a significant environmental burden as processes are less optimized than upstream steps and scales are larger than downstream steps. By shining a spotlight on these early stages, we can orchestrate a symphony of sustainability improvements.
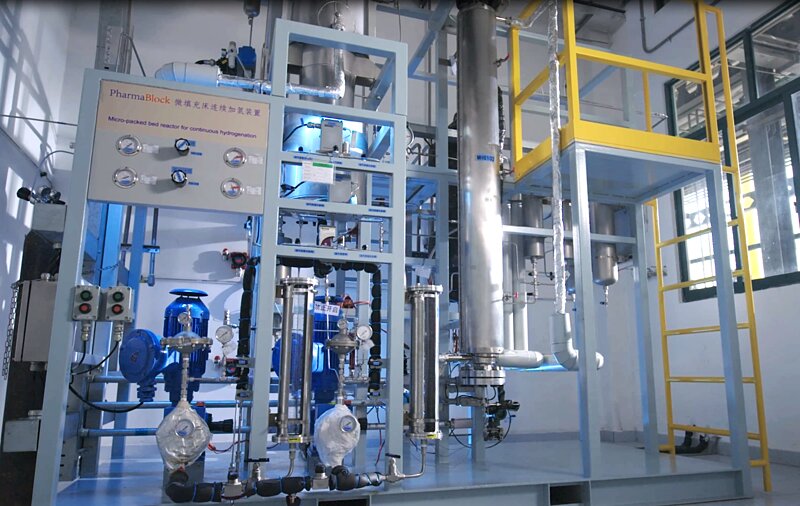
A Glimpse of Continuous Flow Chemistry Technology
CFC technology involves pumping reactants into a singular chamber, tube or microreactor at precise flow rates, where the reaction occurs as the fluids interact within the reactor. CFC technology in pharmaceutical manufacturing features reduced reaction times, higher selectivity, straightforward scalability, safe handling of hazardous intermediates, resulting in improvements in process mass intensity (PMI, to evaluate the efficiency and sustainability of a manufacturing process), energy efficiency, workspace and workforce efficiency. It also has the potential to boost cost-effectiveness, making it an appealing option for sustainable manufacturing.
One of the standout applications of flow technology is in hydrogenation with micropacked bed reactors. Hydrogenation is widely used in the pharmaceutical industry, but often present challenges leading to environmental and safety concerns. A pivotal accomplishment of PharmaBlock’s 2024 award-winning endeavor is the application of micropacked bed technology in hydrogenation and oxidation reactions to achieve a safer, more efficient and greener alternative.
Unveiling PharmaBlock’s Innovations in Continuous Flow Chemistry
Equipment Innovation for Flexibility
The widespread application of continuous flow chemistry technology in the pharmaceutical industry, particularly in intermediate development and manufacturing, has been slowed by challenges related to flexibility. Different chemical reactions have diverse needs regarding temperature, pressure and handling hazardous materials. PharmaBlock showcases its engineering expertise through the design and assembly of flow reactors that provide high flexibility. Our team of mechanical, electronic and automation engineers has developed reactors in various volumes and materials to accommodate more than 50 types of reactions.
The company is even planning to expand its impact by commercializing some of its technologies and equipment, making their innovative technology accessible to the entire industry.
Equipment Innovation for Industrial-scale Application
PharmaBlock aims not just to develop innovative solutions in the lab, but to upscale its technology for industrial manufacturing. Equipment design innovations facilitate the smooth transition from development to full-scale production, a crucial step in bringing new drugs to the market both swiftly and cost-effectively.
For example, photo reactions, traditionally difficult to scale up, can now be implemented with ease thanks to PharmaBlock’s photo flow reactors. These reactors can achieve up to 100 kg per day output, providing process chemists with the flexibility to utilize this green reaction.
The company’s continuous manufacturing area, outfitted with micro-channel and continuous tubular reactors, supports a range of reactions, including low-temperature, high-temperature, high-pressure, nitration, oxidation and Curtius rearrangement reactions.
Innovative Application for Challenging Chemistry
PharmaBlock has excelled in hydrogenation, using a continuous flow process with micro-packed bed reactors. They moved beyond lab scale, designing equipment for manufacturing-scale that can achieve yearly outputs of hundreds of metric tons. This benefited over 70% of manufacturing projects involving hydrogenation, including the 2024 ACS Green Chemistry Awarded project, and a few commercial RSM projects.
Furthermore, PharmaBlock has innovatively applied continuous flow technologies to eliminate the traditional batch process for nitration in pharmaceutical production. By improving thermal control and safety measures, and reducing waste, the team has made this corrosive process more efficient and eco-friendly.
Integration of Biocatalysis and Flow Technology
Biocatalysis, another sustainable technology, has also been widely applied in PharmaBlock. To further exploit the opportunities, several strategies and technologies have been developed, such as the use of immobilized biocatalysts to enhance their stability and recyclability, combining immobilized biocatalysts with flow technology to achieve more sustainable manufacturing process. The increasing mastery of biotechnology allows PharmaBlock to develop enzymes and green process that can synthesize a widening selection of desirable bulk chemicals at commercially viable productivities.
Innovation in Creation of Sophisticated System to Achieve Real Continuous Manufacturing
Another significant advancement in our technology is the ability to create sophisticated systems capable of multi-stage continuous flow manufacturing, including complex workup processes, in a continuous flow system. Combined with an automation setup, it brings us closer to the ideal of true continuous manufacturing, a considerable challenge in the field. This advancement led to the 2023 ACS Green Chemistry Award. The innovative process involves continuous decarboxylation, decolorization, extraction and separation, for producing 3-oxocyclobutane-1-carboxylic acid.